A concrete mixing plant is an electromechanical device that is mainly used to measure and mix raw materials such as cement, water, aggregates, admixtures and additives according to a specific concrete mix ratio, and finally produces concrete that meets quality standards. It is widely used in many industries such as roads, bridges, buildings and infrastructure construction.
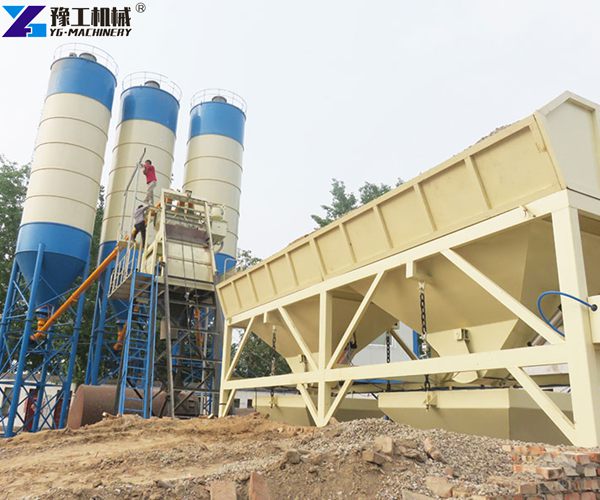
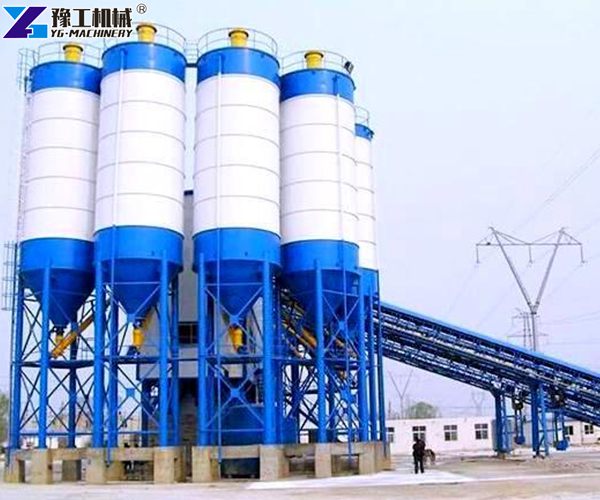
Main components of a concrete mixing plant
Mixing system
The mixing system is the core of the entire mixing plant, which consists of a mixing main unit and is usually divided into two types: forced mixing and self-falling mixing.
- Forced mixing: Suitable for mixing dry hard concrete, fluid concrete, lightweight aggregate concrete and mortar, with high mixing quality, short time, low energy consumption and low noise.
- Self-falling mixing: Suitable for plastic concrete, but less used in industrial applications.
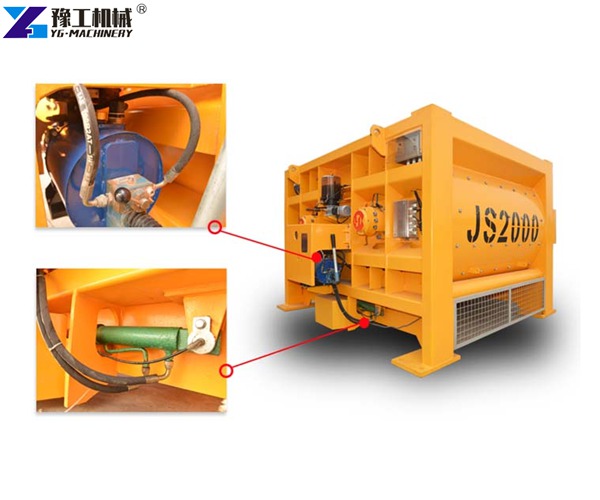
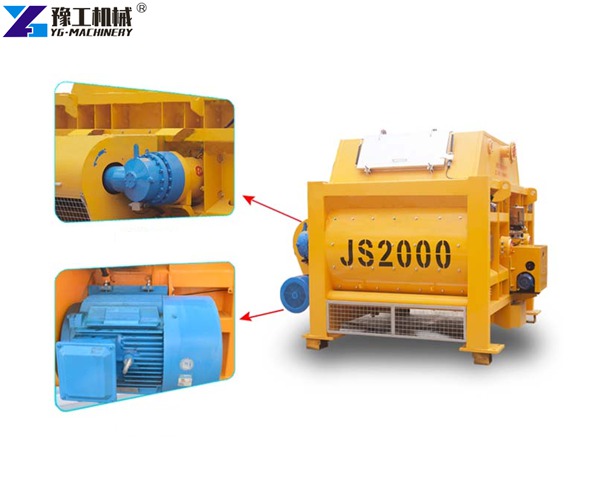
Batching system
The batching system is used to accurately measure various concrete raw materials, usually including the following parts:
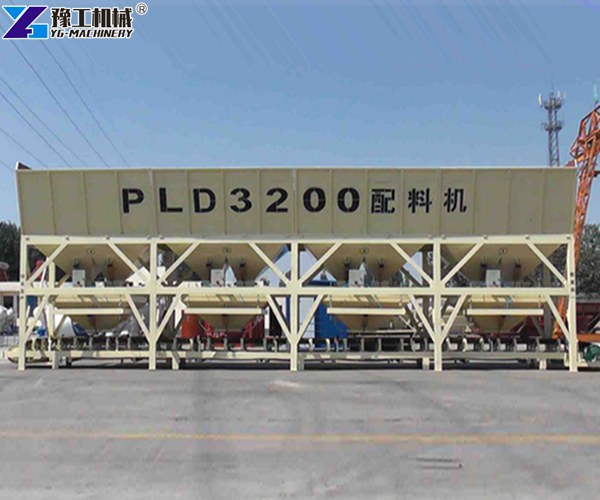
- Admixture silo and admixture metering system
- Aggregate silo
- Aggregate metering system
- Water silo and water metering system
- Cement silo and cement metering system
Material weighing system
The material weighing system consists of three parts:
- Aggregate metering (accumulated weighing or single weighing)
- Powder metering (for cement, fly ash, etc.)
- Liquid metering (water and admixture)
Conveying system
The conveying system is used for material transmission, among which aggregate conveying often adopts flat belt mode, with low failure rate and high reliability.
Control system
The control system is responsible for the automatic control of the entire production process, including batching ratio, metering accuracy, batching sequence, etc. It usually adopts microcomputer automatic control system and can be equipped with printing system and monitoring equipment.
Working principle of concrete mixing station
- Power-on initialization: After the system starts, enter the human-computer interaction interface and set the parameters such as formula number, concrete grade, slump, and production volume.
- Material preparation: Aggregates are stored in aggregate silos, and cement and other powder materials are stored in powder silos.
- Material transportation and metering:
- Start the transportation system to transport fly ash, cement, etc. to the metering equipment.
- Open the water silo, mix the admixture with water and flow it into the metering hopper.
- According to the set ratio, automatically weigh and meter various materials.
- Mixing: Send the prepared materials into the mixer for mixing.
- Discharging: After the concrete mixing is completed, unload it to the concrete tank truck or use it directly.
Key factors for purchasing concrete mixing station
Production capacity
Different engineering requirements correspond to mixing plants of different specifications. Generally classified by production capacity:
- Small mixing station (≤50m³/h): Suitable for small projects or temporary construction projects.
- Medium mixing station (50-150m³/h): Suitable for municipal construction and real estate projects.
- Large mixing station (≥150m³/h): Suitable for highways, large infrastructure and other projects.
Degree of automation
Concrete mixing plants uses automated control systems. High automation can improve production efficiency and reduce labor costs.
Equipment quality and brand
It is recommended to choose a brand with high market recognition and pay attention to the mixing efficiency, metering accuracy and failure rate of the equipment.
Environmental performance
Environmental protection regulations are becoming increasingly stringent. Choosing a mixing station with low noise and low dust emissions can reduce environmental problems.
Maintenance and care
Daily inspection
- Check whether the mixer, sensor and conveying system are normal.
- Observe the metering accuracy of the batching system to ensure that there is no error.
Regular maintenance
- Clean the accumulated material inside the mixer to prevent agglomeration.
- Maintain the conveyor belt to prevent wear and tear from affecting production.
- Replace severely worn parts in a timely manner.
Conclusion
As a key equipment in modern construction projects, concrete mixing plants need to consider production capacity, automation level, environmental performance and brand quality when purchasing. At the same time, reasonable maintenance and care can effectively extend the life of the equipment and improve production efficiency. With the development of intelligent and environmental protection technologies, future concrete mixing plants will be more efficient, environmentally friendly and intelligent, helping the sustainable development of the construction industry.